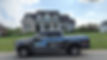
Home Energy Audit
Don't be fooled by "free" energy audits offered by HVAC and insulation companies, as they are typically used as a sales tool to sell you whatever the company offers. There is little incentive for them to truly test and diagnose your issues, since the real solutions may be things other than what they provide.
Our "standard home energy audit" includes an air-leakage test on the house with a "blower-door system", a duct-leakage test, an infrared thermal scan of the surface areas of the building, along with a visual inspection of all areas inside and outside of the home. A summary report with recommendations for improvements is then emailed to the customer upon completion. If a more detailed inspection is needed, we have options to dig further!
This allows us to simulate air-leakage on your house to see how leaky it is, compared to other similar houses. It's really the "starting point" in the energy audit and it can quickly determine how much improvement is possible by air-sealing the house.
There are several ways we can test how much air leaks out of your ductwork, and finding leaky or disconnected ducts can uncover big opportunities to improve comfort, indoor air quality, and overall HVAC efficiency.
HVAC System Performance
Your heating and cooling system is much more than just the box that creates hot or cold air. The ductwork connected to it and the way its designed are crucial to it's performance. Testing for air-flow, static pressure, heat-rise, and cooling-drop are needed to uncover problems.
We do thermal imaging with infrared cameras in Kentucky and Indiana, primarily to find problems in buildings that result from heat loss or gain, air-leakage, water leaks, and "hot spots" in circuits and electrical distribution systems.
Visual Inspection
Without eyes on the problem areas, its hard to recommend what improvements are needed. We check all areas inside and outside the home that are accessible, and take a close look at HVAC and water heating systems for signs of deterioration.
Health & Safety
Gas furnaces, water heaters, and stoves can create unique health & safety issues if they aren't installed or operating properly. Testing for gas leaks, proper flue-draft, and carbon monoxide leaks is very important on any improvement project.